Designing for Strength: What to Consider in Plastic Part Design
How to design parts for strength
One of the more difficult questions I get asked by our customers is how to optimize assemblies for strength. This is an incredibly complex question but an important one when it comes to product development. Simulations like Finite Element Analysis are always a helpful tool, but FEA only provides some of the information, not all of it. Here are some questions to begin with during the development process:
How will the assembly be joined?
Most plastic parts get assembled with other plastic, metal, or electronic components like circuit boards or LEDs. So, we first identify what technology is best to weld or rivet the parts together. If the assembly needs an airtight seal, welding is probably the right choice. If parts are dissimilar materials, staking or riveting is a cost-effective option.
How will it be used?
Customers or industries often have requirements that should be able to direct some of these questions. Will the assembly undergo dynamic stresses like cyclic loading, vibration, or impact? Long-term, steady temperature exposure or swift thermal expansion and contraction? How do those impact the design?
Will the parts have stress built in?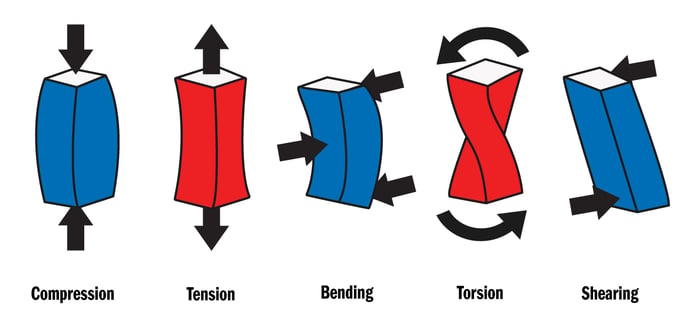
In other words, will the assembly have internal stresses due to material selection or mold process parameters? Will the part be warped and then put back to "CAD" by the joining process?
How accurate will the parts be?
Holding tight, repeatable dimensional tolerances is the most common variable our customers face. This may have assembly implications that often need to be dealt with in tooling or operator assembly and can influence durability or performance.
An electronic assembly example
So, back to the question – how do I design my part? Here is an example we often encounter – staking/riveting a board to a plastic housing. Suppose our customer is an automotive supplier, and their part is a control module in a plastic enclosure. The PCB and a heat sink need to be staked to the housing. The vehicle manufacturer will have standards for mechanical shock, impact testing, chemical testing, and more.
For this example, let's look at temperature vibration testing, which is a combination of dynamic and thermal stresses. Overall part performance is a function of the number of bosses, internal stresses within the part (how twisty), stresses due to thermal expansion and contraction, and forces due to moving mass (mass multiplied by acceleration). To break that down:
Account for temperature fluctuations.
Consider internal stresses due to changes in material characteristics with varying temperatures, such as frigid temps like -40 C. This includes increases in resonance, varying expansion-contraction rates, etc. This may mean the board needs slotted holes or larger through holes.
Address twisting and bending conditions.
Consider twisting, bending, or other internal stress conditions due to inconsistent forces.
Analyze forces from acceleration.
Consider the forces due to the acceleration of the part to be attached. Suppose the PCB and heat sink is 150 grams (about half the weight of a can of soup), and the vibration profile is a 10GRMS random body profile; With F=ma, that's 1.5 Newtons. However, this force doesn't consider resonances, so if there's a resonance characteristic, the force could be even higher. To account for this, use Finite Element Analysis (FEA) to model and predict how the part responds to vibration, leading to an increased acceleration and force.
Evaluate strength as a percentage of parent material strength.
Take the sum of those stresses and consider the parent material strength of the plastic needed to hold the part that is staked to the plastic. All three axes need to be considered, along with torsional, sheer, and bending to the bosses. Design the boss cross-sectional area and determine the number and placement of the bosses based on those factors. Consider strength reduction due to staking. Extol's staking products can optimize the boss for strength, but we know that any staking technology has a lower percentage of strength than parent material (typically 70-90%).
Apply a safety factor.
Put a safety factor on all that to ensure reliability and cover unforeseen variability.
Let us help you!
This is a broad example, but it shows a bit of the thought process of designing for strength. For more information on plastic welding or staking technologies, send us a note using the form below. We'll connect you with one of our plastic assembly enthusiasts to answer any welding and staking questions you have.